At the beginning of 2015, the Production Innovations Network (PIN) was spun off from the Collaborative Research Centre “Gentelligent Components in their Lifecycle“. With PIN, the fundamentals provided by the CRC for a Industry 4.0 compliant networked production are put into practice.
Aim of the network is to promote the dialogue between engineers, manufacturers, users and researchers and to initiate joint projects among industry companies and with science. What are the demands of industry? What is possible with today’s research? Which gaps between research and practice have to be bridged? These are the questions to be solved by PIN, in order to implement digitized and networked production into application-oriented projects tailored to the market needs. The main goal of the Production Innovations Network is to derive elaborated strategies from individual Industry 4.0 applications and to make networked small- and medium-sized enterprises fit for the future in terms of Industry 4.0.
The history: On 15th January 2015, more than 70 companies came to the Hannover Centre for Production Technology of Leibniz Universität Hannover to see live in the test fields what is already possible with Industry 4.0 applications developed from fundamental research. Another topic was to discuss how companies can successfully face the massive modifications coming in the future. Apart from eleven research institutes, the PIN currently consists of twelve associated companies and the IHK Hannover (Hannover Chamber of Industry and Commerce) as sustaining member.
The kick-off: At the first meeting on 29.04.2015, the research institutes of PIN presented their expert reports concerning Industry 4.0, and the companies presented their Industry 4.0 related demands, competences and resources. Two working groups - with the focus on production and maintenance – worked out six main topics:
1. Sensor technologies / (distributed) pre-processing
Collecting data is the basis of Industry 4.0 on the road to digital economy. Gathering new information is one essential part, especially in the field of production. In the PIN we use sensors which are either manufactured on the component surface or which are based on thin foils of a few micrometres. These methods increase the sensitivity by the factor of 15. Due to their small size and their manufacturing method, a completely new positioning of the sensors is possible – for example in grooves or on extremely bent surfaces.
2. Communication / power supply
Especially in case of moving components, reliable wireless data transmission is indispensable. The components’ uninterrupted power supply must be guaranteed. How can optical fibres be perfectly integrated in a machine tool environment? What about the potentials and possible applications of high frequency radio communication, autonomous radio cells in the 24 GHz range in metallic structures? The PIN is working hard to find solutions.
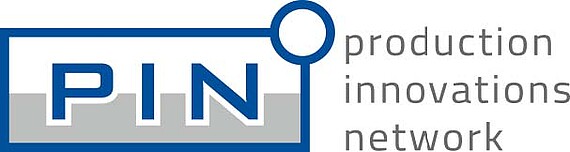
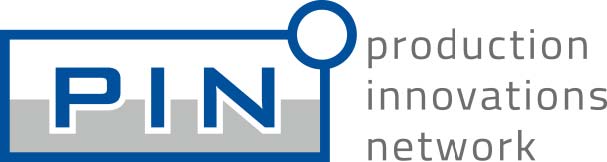
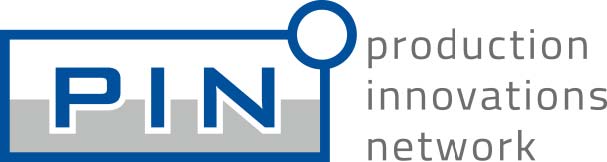
3. Data evaluation (Big Data / machine learning)
Data are only of economic value when used appropriately. The PIN develops evaluation methods for various applications that are tailored to suit the market need. In combination with the know-how of eleven research institutes, the members’ expertise offers expert knowledge covering the whole value chain of production technology. This knowledge base in conjunction with real demands of industry gives the PIN the potential to transform machine and production data into knowledge and develop autonomous process optimization and planning capabilities.
4. Intelligent data combination
Knowledge gained from data has to be utilized in order to be able to make decisions. Assistance and autonomy are the key terms for an intelligent combination of data with the aim to gather new information for decision making. Both aspects, assistance and autonomy, are investigated at the PIN.
5. Standardization / safety
Where components interact, standards are needed to provide for flexible integration. As digitalization requires a high level of reliability, the PIN also focuses on the protection against tampering and plagiarism as well as on the protection of personal privacy.
6. Employee trainings, working environments, legal aspects
In the factories of tomorrow, humans will continue to play a prominent, though changed role. The PIN deals with the new demands on work and people as well as with the options to provide them with optimum assistance.
Current projects
In 2015, the PIN launched three projects. The main questions are: Which data are needed by the end users? Which are the members’ existing user interfaces?
Industry 4.0 check-ups: The PIN gives PIN partners industry check-ups, in order to identify Industry 4.0 relevant demands, expertise and potentials. Then, either implementation or development projects are developed from the check-up results.
Implementation projects shall be realized based on the partners’ expertise and potentials. In the best of cases, no extra research is required. In case of gaps, which can only be filled with extra research effort, long-term (development) projects will be initiated and financed through funding programmes (ZIM-funded projects, DFG-funded projects, etc.).
Demonstrator project – Data collection: The project for data collection in a real production process is either implemented at an end user’s site or at the Institute of Production Engineering and Machine Tools. The project includes data fusion, i.e. the integration of production machine data and the corresponding quality assurance data into a data pool for process and quality data correlation. After data fusion, a cost-benefit analysis is made, and gaps of conventional technologies are identified. Within the PIN, the data are provided for analysis and visualization.
Interactive maintenance: The mobile solution for interactive maintenance is to provide interactive information which is required to correctly perform maintenance measures on manufacturing systems. In the project, QR codes on system components are captured visually for localization and identification, and visual identification marks are projected via data projector or laser to assist the respective process steps. The user navigation is supported by a speech output of the handling instructions. It is individually configurable and can also be used for the training of unexperienced staff. The aim is to make staff assignment more flexible. Unexperienced staff receives much assistance from the system. In the course of the learning process, assistance is more and more reduced, in order not to slow down routine work flows. Integrating manufacturing data for condition based maintenance as “Predictive Maintenance“ is generally possible.
Further topics of long-term development projects include:
- High-flexibility sensory clamping system for the monitoring of welding and machining processes
- Direct structuring of sensors on functional components
- High-speed radio communication in machine environments
- Efficient quality
- Matching planning